Maß- und Formbestimmung von flächigen Objekten
In vielen Industriebereichen wie auch in der Papier-, Druck- und Druckweiterverarbeitungsindustrie, stellt sich, verbunden mit ständig anwachsenden Qualitätsansprüchen, immer wieder die Frage nach Maß- und Formhaltigkeit sowie -treue von flächigen End- oder Zwischenprodukten. Die meisten Verarbeitungsmaschinen nutzen ein oder zwei Materialkanten des Verarbeitungsgutes als Anschlag und damit als maßliche Nullreferenz für den folgenden Verarbeitungsschritt. Stimmt diese Nullreferenz aufgrund zuvor stattgefundener Verarbeitungsprozesse nicht, kann das zu Verarbeitungsproblemen, zu Einbußen der Qualität des Endproduktes, bis hin zu Ausschuss führen.
Bedeutende Auswirkungen auf den Fertigungsprozess
So ist z.B. der rechtwinklige Beschnitt von Bedruckstoffbogen eine wichtige Voraussetzung dafür, dass bei Transport und Verarbeitung die angestrebten Qualitätskriterien z.B. hinsichtlich des Anlage- und/oder Wendepassers in Druckmaschinen, der Falz- oder Stanzgenauigkeit erreicht werden können. Beim Einsatz neuartiger Technologien wie z.B. beim digitalen Stanzen mittels Laser oder Wasserstrahl sind zusätzlich Schwankungen in den Abmessungen nacheinander hergestellter Exemplare möglich, die eine deutliche Qualitätseinschränkung bedeuten können.
Diese messtechnischen Aufgabenstellungen lassen sich darauf zurückführen, die Lage eines Objektes oder eines Teiles davon relativ zu einem anderen Objekt zu bestimmen. Abhängig vom Prozess spielen dabei die erforderliche Genauigkeit, die Objektgröße und Objekteigenschaften bei der Wahl der eingesetzten Mittel eine entscheidende Rolle.
In der grafischen Industrie kommen zu diesem Zweck üblicherweise Messelemente zum Einsatz, die auf das zu vermessende Objekt als Messmarke aufgedruckt werden und deren Lage mittels optischer Sensoren vermessen wird. Dazu sind spezielle Ausformungen von Messelementen und Messmarken sowie Auswerteverfahren entwickelt worden, die hohe und sehr hohe Messgenauigkeiten im Bereich weniger Mikrometer erreichen.
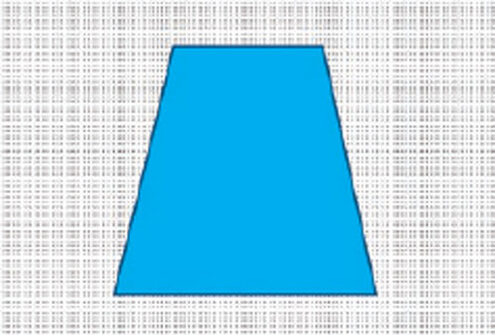
Aufgrund einer oft benötigten Vielzahl an erforderlichen Messorten und anfallenden Messdaten ist es weiterhin auch außerordentlich nützlich, wenn das Messelement oder die Messmarke neben den primären Ortsinformationen noch weitere Informationen tragen kann, die von einer automatischen Messeinrichtung extrahiert werden können. Dies können z.B. Daten zur Herkunft des gedruckten Messelements oder Messmarke (z.B. Druckwerk, Seite, Position, Auftrag, etc.) sein.
Positionsbestimmung mit dem LUCHS IV-Sondermesselement
Mit dem vom SID entwickelten Passermesssystem LUCHS IV ist der Anwender mit der Option "Sondermessung" z.B. in der Lage, die Position von Kanten des Bedruckstoffes (Schnitt- oder Falzkanten) relativ zu einem gedruckten Messelement zu bestimmen. Führt man diese Positionsbestimmung an mehreren Exemplaren durch, welche die Verarbeitungsmaschine (z.B. Druck-, Falzmaschine) nacheinander verlassen, lassen sich damit anhand der Schwankung Rückschlüsse auf Verarbeitungsparameter und Verarbeitungsmaschine ziehen.
Der Struktur des verwendeten Sondermesselementes wohnt ein metrisches Koordinatensystem inne, welches mit Methoden der Bildverarbeitung ausgelesen wird und zu welchem die Bedruckstoffkante in Bezug gesetzt wird. Die derzeitige Ausführungsform eines solchen Messelementes umfasst einen Messbereich von maximal 27 x 27 mm.
Möchte man die Lage der Bedruckstoffkante an mehreren Stellen auf dem Exemplar ermitteln, muss für jede Messstelle ein separates Messelement verwendet werden, wodurch ein gemeinsamer Bezug im Sinne eines gemeinsamen Koordinatensystems verloren geht.
Einschränkungen der jetzigen Technologie
Das als "Sondermessung" beschriebene Verfahren ist heute für verschiedene Anwendungsfälle im praktischen Einsatz, hat jedoch wie oben bereits angedeutet verschiedene Beschränkungen und Rahmenbedingungen, die einen breiteren Einsatz dieser Lösung und eine reale Ermittlung von Abmessungen und Formen nicht zulassen.
Die wichtigsten dieser Limitierungen sind nachfolgend aufgeführt:
- Für die "Sondermessung" sind grundsätzlich Messmarken auf ein Medium aufzudrucken. Objekte ohne Bezug zu solchen Messmarken können grundsätzlich nicht vermessen werden, was eine Vermessung von Rohmaterialien oder Anwendungen in anderen Industriebereichen außerhalb der Druckindustrie ausschließt.
- Auch in der grafischen Industrie sind die Einsatzmöglichkeiten der "Sondermessung" begrenzt, da die Messelemente aufgrund Ihrer Größe (27 x 27 mm) in der Regel nicht im üblichen Produktionsprozess mitgedruckt werden können. Es ist deshalb meist eine Testdruckform zu verwenden und eine Kontrolle von Druckprodukten aus der laufenden Produktion somit nicht ohne weiteres möglich.
- Das Verfahren der "Sondermessung" im Druckbereich ist gleichfalls nicht dazu geeignet, maßliche Veränderungen, die nach dem Druck der Marken am Bedruckstoff entstehen, zu erfassen. So können beispielsweise Papierdehnungen oder -schrumpfungen die unter anderem durch Feuchtmitteleinflüsse oder Klimaveränderungen entstehen, nicht erfasst werden, da sich die Position der aufgedruckten Marken mit dem sich verändernden Bedruckstoff mitbewegt, jedoch kein gemeinsamer Bezug verschiedener Marken zueinander in einem gemeinsamen Koordinatensystem existiert.
Die oben aufgeführten Beschränkungen zeigen, dass für die genaue Ermittlung der Maß- und Formhaltigkeit von flächigen Objekten bisher in vielen Fällen keine in der industriellen Praxis einsetzbaren Lösungen existieren. Technisch eventuell nutzbare Koordinatenmesssysteme scheiden aus wirtschaftlichen Gründen aus. Darüber hinaus ist deren Einsatzbarkeit für sehr dünne Materialien, zum Teil im Bereich von 0,02 mm Dicke, fragwürdig.
Im Bereich der Papier-, Druck- und Druckweiterverarbeitungsindustrie aber auch in vielen anderen Industriebereichen, in denen flächige, zum Teil flexible und sehr dünne Materialien verarbeitet werden, ist die Bestimmung der Abmessungen und der Formhaltigkeit einzelner Objekte eine außerordentlich wichtige Aufgabenstellung. Die Aufbringung von Messmarken auf dem zu vermessenden Objekt ist dabei in vielen Fällen unmöglich. Deshalb wurde nach einer Lösung gesucht, die darauf verzichtet. Die Bestimmung von Kanten oder Punkten eines Objektes in einem gemeinsamen Koordinatensystem ist möglich und eine kontaktlose Messwerterfassung sichergestellt, um flexible oder komprimierbare Materialien beim Messvorgang nicht zu deformieren. Einsatzgebiete für solche Lösungen sind neben der Papier- und Druckindustrie unter anderem die Verpackungsherstellung, Stanz- oder Schneidvorgänge flächiger Materialien wie Papier, Karton, Wellpappe, Textilien oder beliebiger anderer Faser- und Vliesstoffe.
Entwicklungsziele des Projektes
Zielstellung des Projektes war die Entwicklung eines hochpräzisen Messsystems zur Bestimmung von Abmessungen und Formhaltigkeit dünner, flächiger Objekte, das auf der intelligenten Auswertung eines großen, zweidimensionalen Messelements basierte. Im Unterschied zu bisherigen Lösungen ist dieses Messelement jedoch nicht auf das jeweilige Messobjekt aufzubringen, sondern wird auf ein weitestgehend dimensionsstabiles Substrat übertragen, das eine für die Anwendungsfälle ausreichende Größe haben kann. Dieses Substrat mit dem aufgebrachten Messelement bildet praktisch die Referenz für alle Maß- und Formbestimmungen eines auf diese Referenz aufgelegten Prüfobjektes.
Die zu Grunde liegende Idee war die Positionsmessung signifikanter Begrenzungspunkte eines flächigen Messobjektes, das in Bezug zu dem erwähnten Messelement gebracht wird. Signifikante Begrenzungspunkte beispielsweise eines Papierbogens sind dessen 4 Eckpunkte, die Aufschlüsse über die Grundmaße und die Winkel zulassen. Sind weitere Auswertungen, z.B. über die Geradlinigkeit der Schnittkanten gefragt, müssen an den Kanten weitere Messpunkte hinzugezogen werden. Eventuell sind zu den Begrenzungspunkten oder dem Messobjekt weitere Angaben notwendig, vor allem dann, wenn die eindeutige Signifikanz bestimmter Begrenzungspunkte nicht gegeben ist (z.B. kreisförmig oder oval gestanztes Verarbeitungsgut wie Bieruntersetzer).
Für die Messung eines Begrenzungspunktes ist ein Bild notwendig, welches nur die Kontur des Messobjektes an jenem Punkt und einen Ausschnitt des Messrasters enthält. Mit Hilfe der Informationen aus dem Messraster kann die Position des Begrenzungspunktes in metrischen Koordinaten ermittelt und festgehalten werden. Die Erzeugung des Bildes erfolgt hierbei mit einer handlichen Einrichtung, die eine Kamera enthält (spezieller Messkopf oder Mobiltelefon mit Kamera und Aufsatz). Das hat den Vorteil, dass auch sehr große Formate, so sie innerhalb des untergelegten Messelementes liegen, sehr präzise vermessen werden. Nachteilig daran ist, dass bei einer höheren Anzahl zu messender Begrenzungspunkte, der zeitliche und personalbindende Aufwand steigt. Um diesen Nachteil zu umgehen, wäre die Aufnahme eines Bildes vom gesamten Messobjekt auf dem Messraster notwendig. In nachfolgenden Bildverarbeitungsschritten müsste dann die Kontur des Messobjektes erfasst werden und diese dann mit Hilfe der Informationen aus dem Messraster in metrischen Koordinaten umgerechnet werden. Die Vorgehensweise der Gesamtbilderfassung hat bei kleineren Messobjekten besonders bezüglich des Aufwandes sicherlich Vorteile. Dabei ist aber davon auszugehen, dass die Auflösung des unterlegten Messrasters gröber sein muss, als das bei der Einzelmessung der Begrenzungspunkte ist. Hinzu kommt die sphärische Verzerrung durch Linsenfehler oder nicht parallele Ausrichtung des Bildobjektes zur Abbildungsebene bei der Bildaufnahme, der durch geeignete Umrechnungsfunktionen von Bild- in metrische Koordinaten entgegengewirkt werden muss. Demzufolge ist die Präzision bei Gesamtbilderfassung geringer.
Bisherige Situation
Mit dem Passermesssystem LUCHS IV ist durch die Verwendung der Option "Sondermessung" die Position von Kanten des Bedruckstoffs (Schnitt- oder Falzkanten) relativ zu einem gedruckten Messelement zu bestimmen. Soll die Lage der Bedruckstoffkante an mehreren Stellen auf dem Exemplar ermittelt werden, muss für jede Messstelle ein separates Messelement verwendet werden. Damit geht ein gemeinsamer Bezug im Sinne eines gemeinsamen Koordinatensystems verloren und das Erfassen einer Kontur oder der Lagebeziehungen bestimmter Konturpunkte höchstens über eine individuelle Auswertung der Messergebnisse des LUCHS unter Einbeziehung der tatsächlichen Positionen der einzelnen Messelemente möglich. Die derzeitige Messkonfiguration der "Sondermessung" schreibt jedoch vor, dass das Messelement auf dem zu vermessenden Bedruckstoff aufgebracht ist. Somit werden sämtliche Fehler des Übertragungsprozesses des Druckbildes (mit den Messelementen) auf den Bedruckstoff dazu führen, dass die tatsächlichen Positionen der Messelemente, wie sie beim Entwurf des Druckbildes als Datei angelegt waren, nun Abweichungen aufweisen können.
Die Zukunft
Mit dem neu entwickelten Messelement in Verbindung mit der Kameraeinheit ist die Vermessung und Erkennung von Formen und Konturen an beliebigen 2-dimensionalen Objekten, z B. an Formatpapieren, Zuschnitten, Stanznutzen, Etiketten mit einer Genauigkeit von Mikrometern möglich.
Zur Vermessung werden das auf einen dimensionsstabilen Träger aufgebrachte Messelement sowie die zu vermessende Kontur des aufgelegten Messobjektes mit einer Kamera abgetastet. Die Kamera nimmt dabei ein Bild von einem Feld auf, in dem ein hinreichend großer Teil des Messelementes und Teile des Messobjekts, der zu vermessenden Kontur, abgebildet sind. Mittels bildanalytischer Methoden wird aus dem Pixelbild das Messelement isoliert und erkannt. Dabei spannt die Bildverarbeitungssoftware ihr eigenes internes Koordinatensystem auf ihrer Pixelfläche auf und ordnet diesem die gefundenen Objekte zu.
Die Möglichkeit, mit dem Messelement ein Koordinatensystem von beträchtlicher Größe herstellen zu können, eröffnet auch insbesondere die Anwendung zur Vermessung der vollständigen Kontur eines Messobjektes in einer Ebene. Das Messobjekt wird dann auf das Messelement aufgelegt und die Koordinaten entlang der Konturlinie werden ermittelt. Die Ausgabe zeigt den Verlauf der Kontur in X- und Y-Koordinaten.
Die Bedienung des Messsystems ist in gleicher Weise komfortabel und einfach wie bei einer Passermessung. Das heißt, es wurde neben der eigentlichen Mess- und Auswertesoftware eine Benutzeroberfläche entwickelt, die eine intelligente Kommunikation zur Beschreibung der Messaufgabe und zu den für die Auswertung benötigten Informationen ermöglicht.
Projektlaufzeit: Oktober 2017 bis April 2020
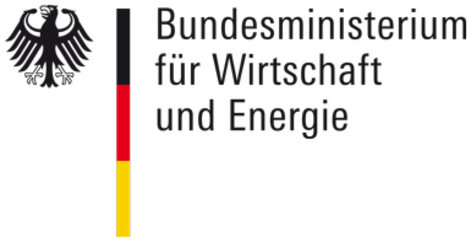
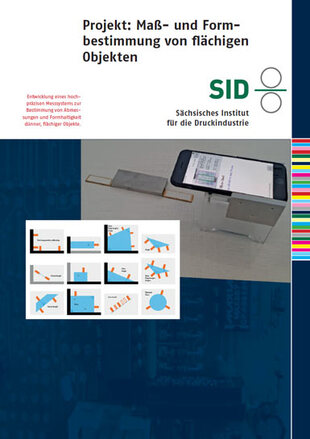
Mehr Informationen im
PDF-Download.