Prozessstandardisierung UV-Offsetdruck
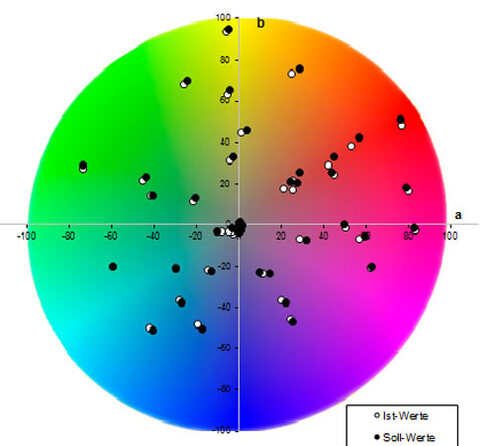
Die durch Bestrahlung mit UV-Licht induzierte Vernetzung von flüssigen Monomeren und Oligomeren sowie den daraus hergestellten Formulierungen ist ein schnelles, leistungsfähiges, effizientes und umweltfreundliches Verfahren zur Herstellung dünner polymerer Schichten. Das Spektrum der Anwendungen solcher Beschichtungen ist überaus breit gefächert und reicht von diversen funktionellen Beschichtungen (z.B. mechanisch resistente Schichten, Barriereschichten, Schutzschichten, selbstreinigende Oberflächen, Release-schichten, Klebstoffe u.v.a.m.) bis hin zu Anwendungen in der Druckbranche (Druckfarben, Tinten und Lacke). In der Druckbranche haben die UV-Farben und -Lacke einen Marktanteil von ca. 10% (Deutschland) bis 20% (Ausland) erreicht, der stark ansteigend ist. Vorteilhaft an diesem Verfahren ist, dass eine große Bandbreite an Bedruckstoffen verarbeitet werden kann und ein hoher Veredelungsgrad (z.B. glänzende, seidenmatte bzw. strukturierte Beschichtung) erreicht wird.
Anwendung im Verpackungsdruck
Zu den bedeutendsten Anwendungsgebieten des UV-Druckes gehört daher vor allem der Verpackungsdruck. Aufgrund des hochwertigen Erscheinungsbildes und der breiten Einsatzmöglichkeiten UV-vernetzbarer Systeme auf verschiedensten – auch nicht-saugfähigen – Substraten stehen dabei vor allem Verpackungsmaterialien für hochpreisige Konsumgüter und Lebensmittel im Vordergrund.
Durch die Entwicklung von neuartigen UV-Strahlern, die im Wesentlichen auf eisendotierten Quecksilberdampflampen (LE-, LEC-, HR-UV) oder LEDs beruhen, werden neben dem Verpackungssektor auch andere Bereiche der Druckindustrie angesprochen. So werden verstärkt Akzidenzdruckmaschinen mit UV-Ausrüstung installiert, die zur Herstellung von Flyern, Plakaten und Geschäftsdrucksachen eingesetzt werden.
Vorteile
Der Einsatz der UV-Technologien im Bereich des Akzidenzdrucks bringt eine Reihe von Vorteilen mit sich:
- Es liegt sofort nach dem Druckvorgang ein (mechanisch) trockener Bogen vor.
- Es ist keine Schutz-Lackierung notwendig.
- Die Farben haben eine hohe Kratz- und Scheuerfestigkeit.
- Es ist kein Puder erforderlich, um das Druckbild zu schützen.
- Es lassen sich hochwertig veredelte Druckprodukte mit hohem Glanz herstellen.
- Insbesondere auf ungestrichenem Papier lässt sich eine bessere Druckqualität erreichen.
- Durch ein erweitertes Angebot von Druckprodukten lässt sich Mehrwert schaffen, um so dem Preiswettkampf zu entgehen.
- Es lassen sich kürzere Lieferzeiten realisieren.
Zusätzlich bringen die neuen UV-Strahler, die gezielt im langwelligen UV-Bereich emittieren, weitere Pluspunkte:
- Es entsteht durch den emittierten Wellenlängenbereich kein Ozon.
- Die Strahler verbrauchen weniger Energie als herkömmliche UV-Strahler.
Diese Vorteile bieten für den Drucker einen hohen Komfort. Dazu kommt bei den UV-LEDs, dass Erwartungen aus dem privaten Umfeld wirksam werden und man sich bei einer Neuinvestition für eine zukunftsorientierte Technologie entscheiden möchte.
Unterschiede zu herkömmlichen Farben
Andererseits birgt die UV-Technologie hinsichtlich der Prozessführung und der erreichbaren Druckqualität einige Herausforderungen. Aufgrund der vollkommen anderen Bindemittelzusammensetzung verhalten sich die Farben während des Auftrags auf das Substrat anders, benetzen und verlaufen anders, dringen anders in das Substrat ein und ergeben einen von herkömmlichen Farben abweichenden visuellen Eindruck. Auch durch genaueste Anpassung der rheologischen Eigenschaften kann das nicht vollständig kompensiert werden. Hinzu kommt, dass für die Rezeptierung andere Rahmenbedingungen wie z. B. das Härtungsverhalten entscheidend sind, so dass bei der Pigmentierung auf ausreichende Transparenz für UV-Strahlung geachtet werden muss, was insbesondere bei Schwarz zu einer vollkommen anderen Färbung führt.
Der wesentliche Unterschied besteht im Farbannahmeverhalten beim Zusammendruck der Farben übereinander. Wird in der üblichen Farbreihenfolge Schwarz - Cyan - Magenta - Gelb gedruckt, so erscheint ein Übereinanderdruck der Volltöne Cyan und Magenta bei UV-Farben rötlicher als bei konventionellen Farben. Diese Unterschiede kommen auch dann zustande, wenn die Primärfarbtöne selbst nahe an den Vorgaben der ISO 2846-1 bzw. im Druckprozess an den Vorgaben der ISO 12647-2 liegen. Das bedeutet, dass selbst bei formaler Konformität zur ISO-Norm bzw. dem ProzessStandard Offsetdruck ein 4-farbig gedrucktes Bild einen anderen Farbeindruck ergibt als erwartet. Zusätzlich erreichen die UV-Farben andere Tonwertzunahmen, die durch spezielle Druckkennlinien kompensiert werden müssen, um die Helligkeit der Rastertöne und insbesondere die Graubalance anzupassen.
Streng genommen müsste für fast jede Materialkombination ein eigenes Ausgabeprofil erstellt werden, da die üblicherweise genutzten ICC-Profile für diese Druckbedingung nicht anwendbar sind. Dies wäre ein extremer Zeit- und Kostenaufwand, den eine Druckerei nur in Ausnahmefällen leisten kann. Deshalb sollte mit dem Projekt der Bedarf nach leicht handhabbaren Profilierungsdaten für UV-Druckfarben sowohl für saugfähige als auch für nicht saugfähige Bedruckstoffe befriedigt werden.
Vorgehen und Ergebnisse
Die Zielstellung des Projekts war die Schaffung von Standardisierungsgrundlagen für den Einsatz von UV-Farben im Offsetdruckprozess. Angestrebt wurde dabei die Angleichung der Druckergebnisse auf verschiedenen Bedruckstoffen an die Qualitätsvorgaben der ISO12647-2 " Graphic technology - Process control for the production of halftone colour separations, proof and production prints - Part 2: Offset lithographic processes". Dabei sollten sowohl saugfähige als auch nicht saugfähige Substrate berücksichtigt werden. Die Optimierung der Farbwiedergabe und durch reproduzierbare Druckergebnisse wurde eine angepasste Farbseparierung erreicht. Im Ergebnis des Projektes stehen speziell geeignete ICC-Profile für den Offsetdruckprozess mit UV-Farben zur Verfügung.
Um dieses Ziel zu erreichen, ist eine angepasste Farbseparierung notwendig, die üblicherweise eingesetzten ICC-Profile können nicht angewendet werden. Im Ergebnis des Projektes sollen speziell geeignete Profile für den Offsetdruckprozess mit UV-Farben vorliegen. Besonderes Augenmerk soll dabei auf eine optimierte Graubalance und einen Schwarzaufbau, der die Probleme der Aushärtung berücksichtigt, gelegt werden. Wichtig ist dabei, dass Materialgruppen zusammengefasst werden, für die das gleiche Profil verwendet werden kann. Hierzu soll ein einfach zu handhabendes Werkzeug entwickelt werden, mit dem die Zuordnung einer unbekannten Materialkombination zu den Profilen ermöglicht wird. So soll vermieden werden, dass eine übermäßig große Anzahl von Profilen für nur geringfügig voneinander abweichende Ausgabebedingungen vorgehalten und gepflegt werden muss.
Für diese Profile wurden die einzuhaltenden Parameter mit entsprechenden Toleranzen beschrieben, sodass die Druckerei transparente Vorgaben zur Qualitätssicherung erhält und einen an das System der ISO-Norm angepassten Produktionsprozess gestalten kann. Diese Vorgabewerte sind zudem geeignet, gelieferte Kundenproofs auch zur Beurteilung der Eignung für den Druck mit UV-Farben zu bewerten. Mit dieser Art der Eingangskontrolle können zukünftig aufwendige Rüst- und Einstellvorgänge an der Druckmaschine und kostenintensive Reklamationen von vorherein vermieden werden. Für Anwendungsfälle, die von keinem der erarbeiteten Profile abgedeckt werden können, wird ein einfaches Prozedere für die Erstellung von Ausgabeprofilen beschrieben, das auf einer vergleichsweise geringen Anzahl von Stützpunkten basiert und keine zusätzliche Kennlinienanpassung erfordert. Dadurch wird ein Maß an Flexibilität erreicht, das weit über die bisher verfügbaren Branchenstandards hinausgeht.
Für die Praxis wird damit sowohl messtechnisch als auch visuell eine hohe Qualität und vor allem eine gute Übereinstimmung der Messdaten mit dem optischen Eindruck erreicht. Zusätzlich ist eine hervorragende Reproduzierbarkeit der Wiedergabequalität gewährleistet, wobei prozesstypische Einflussfaktoren, die die Auflagenstabilität beeinflussen, berücksichtigt werden. Eine permanente Qualitätskontrolle auf Basis der Projektergebnisse ermöglicht jetzt eine Reduzierung der Makulatur und eine Verkürzung der durchschnittlichen Einrichtezeiten.
Projektlaufzeit: September 2018 bis August 2020
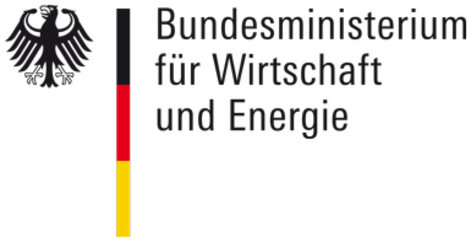